WE ARE EXPERTS IN TECHNICAL PRINTING, CONVERTING AND THERMAL MANAGEMENT
Printing
Depending on the material used and the desired characteristics, Gravic offers several printing processes.
Converting
thermal management
The thermal interface material (TIM) plays a crucial role in any thermal management solution.
Why choose us?
For over 55 years, the Gravic Group has been the strategic partner of the largest industrial groups in the fields of industrial marking, printing and technical cutting.
+55 years Experience
+300 Team of experts
Sustainability and deep care about our environment
Competitive prices
Design partner
0 ppm automotive faults
24 h service
96% on-time delivery
Our Solutions
Gravic offers a wide range of industrial branding and cutting solutions. From front panels to technical labels and thermal management solutions, we also have innovative solutions such as unique labels (e.g. Coca Cola packaging), wood, coated or phosphorescent labels.
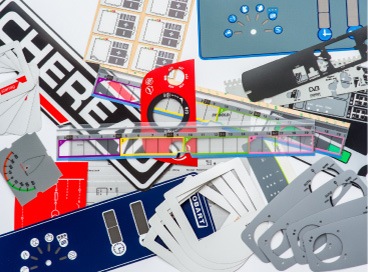
Front panels & Graphic overlays
Used for dashboards, counters, backings, consoles, decorative elements, lecterns, user interfaces, and more.
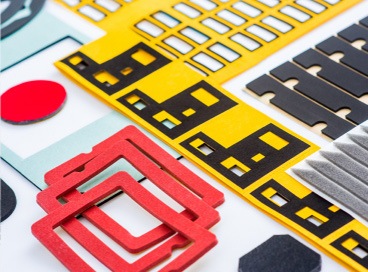
Foam gaskets and Seals
Foam gaskets, foam adhesive, spacers, adhesive stops, pads, insulation, for various functions.
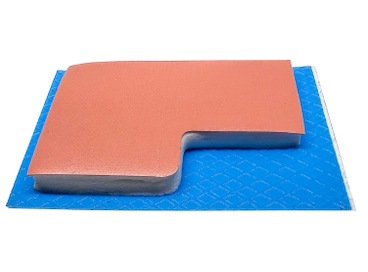
Thermal Management
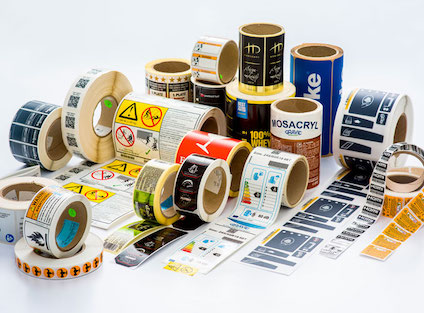
Self-adhesive labels
We produce a wide range of technical self-adhesive labels that can be printed or blank.
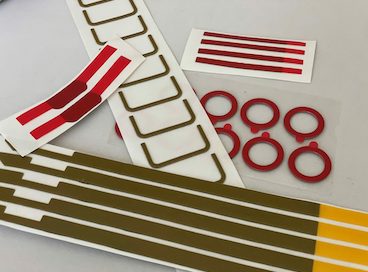
Bonding and Fixing
Tapes and adhesives made in custom shapes and for multiple use, ideal for bonding, sealing and mounting
GRAVIC HUNGARY TURNS 20
Back in 2005, when we opened our plant in Debrecen, we started with just 22 colleagues. It was a small beginning, but we had big ambitions, strong belief, and a shared dream: to build a company where precision is second nature, trust is the foundation…
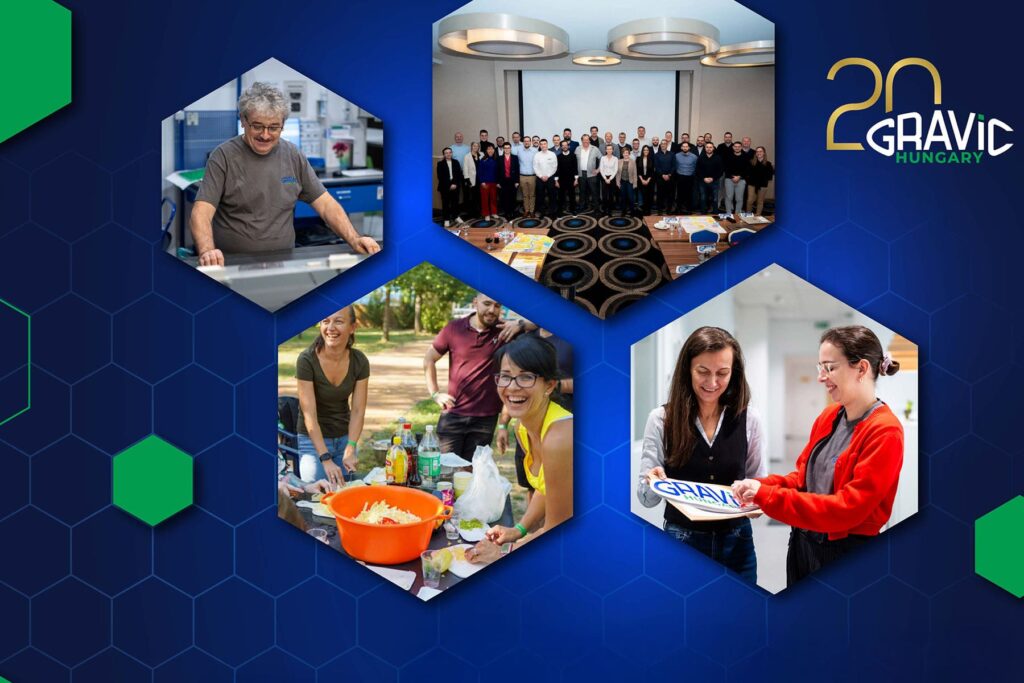
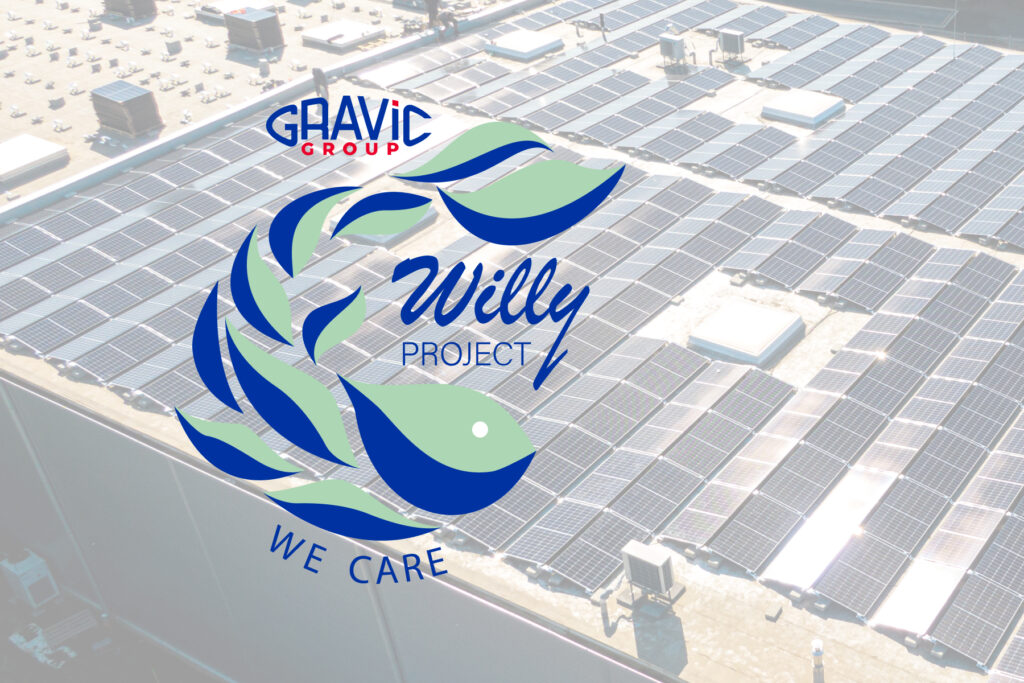
WILLY PROJECT AND OUR COMMITMENT TO SUSTAINABILITY
Read more about how we maintain a healthy community, rely on renewable energy and live in harmony with nature. We are committed to reduce our carbon footprint by 2030.
OUR PEOPLE
Gravic Group’s strength lies in our people when they come together as a diverse family, working towards the same goal as a team. The importance of teamwork cannot be overstated, as it is a fundamental aspect of achieving success.
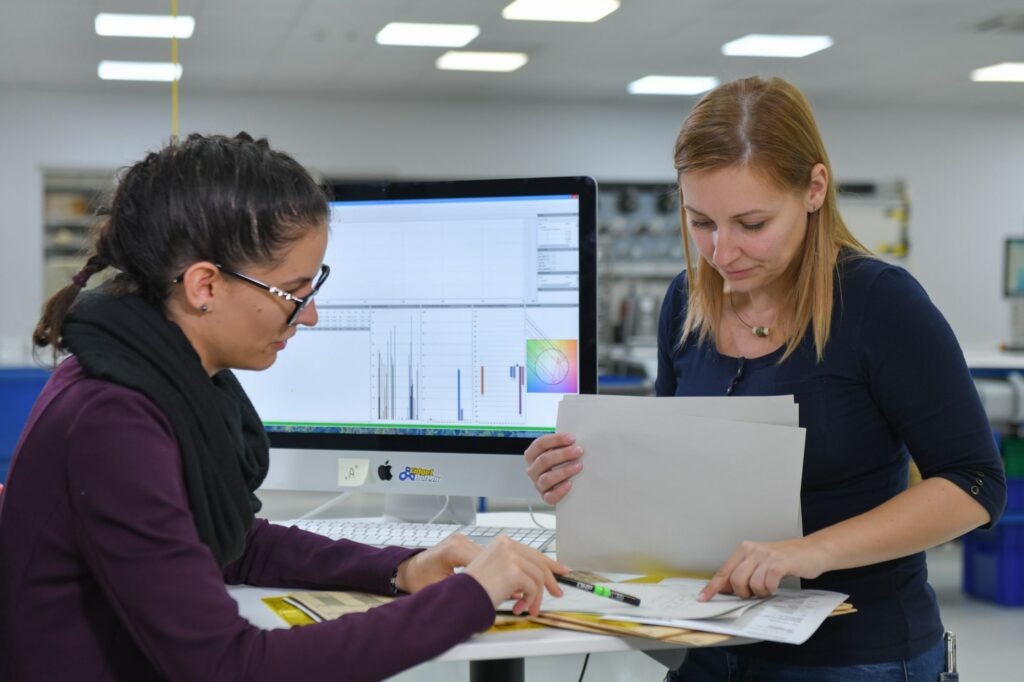
They trust us
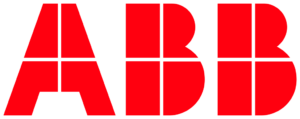
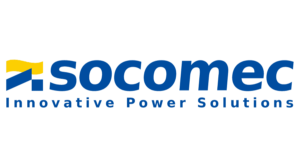
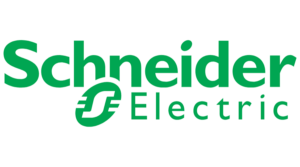
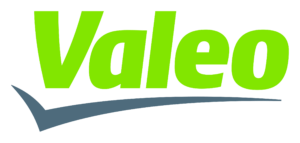
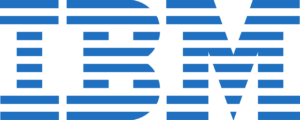
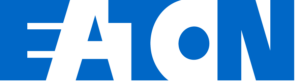
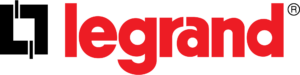
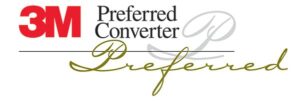
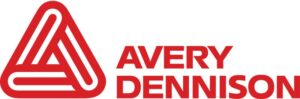
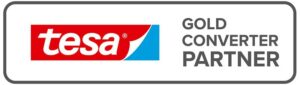
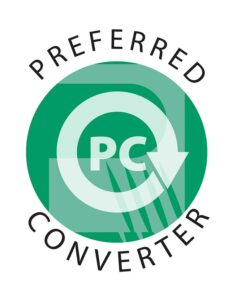
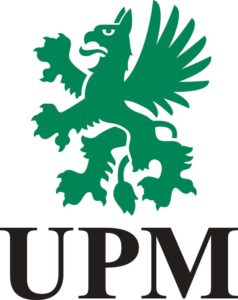
What our customers say...

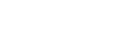
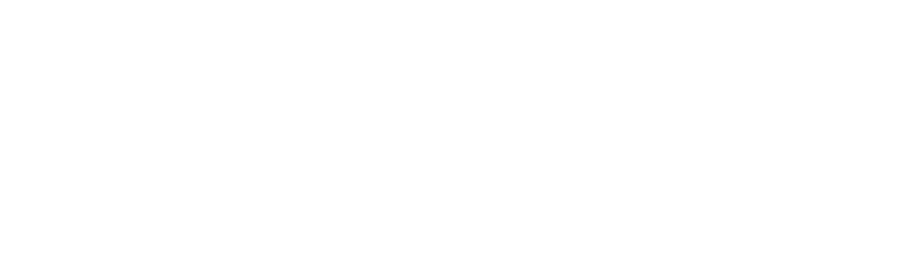
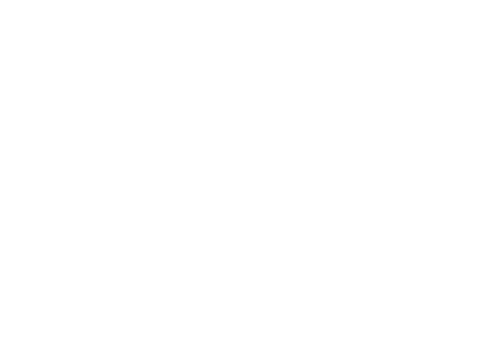
We have been working together since 2015, and we have always got the best service. Professional, ultra kind staff, advanced technology, 100% quality parts.
Go Gravic!"
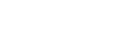
Thank you for this great contribution."
With over 50 years of experience in technical printing and converting, Gravic offers a variety of marking, branding and identification solutions of the very highest quality. You will be sure to find the product that perfectly suits your specifications amidst our wide range of industrial labels: adhesive labels, engravable tags and labels, or 3D labels for identification and branding, security labels to combat counterfeiting and wear, or even electronic RFID tags to assure tracing of your products. Whatever your needs, don’t hesitate to browse through our website or contact us to find the perfect branding or labelling solution for you.
Gravic is much more than a mere label manufacturer: we assist you throughout the production process, including design, printing, cutting, and even lamination of your industrial labels. For example, if you are looking for easy-to-place adhesive labels, or if you are in need of technical labels which can withstand high temperatures and other environmental stresses, we custom-make your perfect labels, and we guarantee fast delivery in the packaging of your choice.
In addition to our industrial identification labels, we also offer die-cutting and printing of technical materials for a variety of uses. Our face plates and back plates can be used as housing and protection for your products, made of a stiff or flexible plastic plate; or for filters for display screens or automotive meters, we offer the full range of die-cutting and printing processes. On our website, you can also find protective and masking films to protect your products during shipping or in use, for example.
To meet your industrial needs for a protective or watertight seal or for electrical, acoustic or thermal insulation, Gravic has developed a range of die-cutting processes for specialist technical materials, such as gaskets, silicon foams, filters, or thermal pads. These essential items for the compliance and safety of your products are custom selected and die-cut in our workshops.
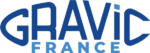
123, Zone Industrielle de l’Argile II, 06370
Mouans Sartoux, FRANCE
Tel. +33 (0)4 93 75 75 34
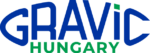
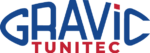
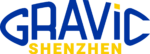
深圳市格瑞维克电子科技有限公司
深圳市南山区南山街道向南社区海德二道470号海德大厦A1002A
Shenzhen, CHINA