Front panels & Graphic overlays
To help you finish your industrial projects, Gravic offers a wide range of technical cutting solutions such as plastic front panel and back panels. From polyester front panels to membrane keypads, you are sure to find the product that suits your specifications.
This type of faceplate or interface is a key element of many everyday products, making them easy to use while protecting their components from external aggressions. Find out more about Gravic’s skills, our expertise in printing and technical cutting, and opt for cut parts which can also be screen printed according to your requirements.
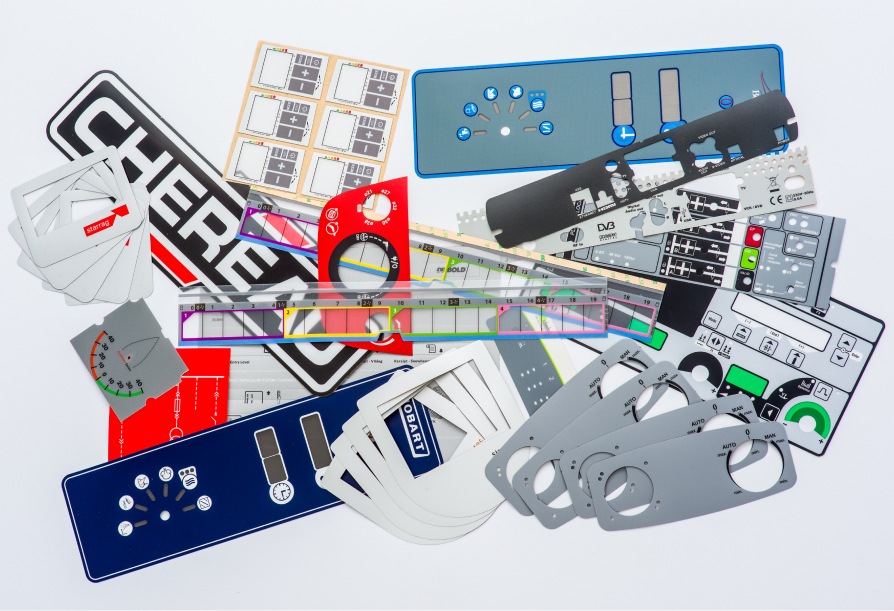
-
Rigid or flexible Front panel and Control panel
-
The front face, also known as a face plate, provides graphical and functional solutions for human-machine interfaces. It can be either a rigid or a flexbile font panel.
The front face contributes to the visual identity of a product, and also provides numerous types of functionality in terms of ergonomics, safety, execution controls, watertight seal, and resistance to external aggressions.
Printing for the flexible or rigid front panel is developed on a transparent plastic film, and placed on the back, which ensures that the colours and markings are optimally preserved over time.
Many choices and criteria are offered to best meet your specifications:
- Look: glossy, matte, satin, grainy, etc.
- Surface treatment: anti-cracking, anti-reflective, anti-UV, anti-vandal, anti-bacterial, etc.
- Tactile functionality: cold or hot embossing for push-buttons, anti-fingerprint enamel, braille enamel, “Soft Touch” enamel, cracking, etc.
- Visual functionality: crystal transparent window display, tinted glazes for LED or backlighting, etc.
- Flexibility: flexible front plate or rigid, depending on the choice and thickness of material (from 75 microns up to 2 cm)
- Adhesive: Depending on the material to which the face plate is affixed, a wide choice of adhesives is available
- Mechanical fixture (inserts, tabs, clips, rivets) or glue
- In-mould injection: Insertion of the front face plate into the mold before injection
-
Graphic Top Cover
- The back face is essential to ensure the functionality of the device, and also makes connections to the device ergonomic. Like the front face, the back face provides an economical solution for screen printing on sheets or pad printing. It is more resistant to cracking and impacts, and provides more flexibility when installing. The back plate offers greater flexibility for multi-lingual and multi-model personalisation of your devices at the end of the production cycle or in after-sales service. Gravic can assist you by offering solutions to assist you in the installation of back plates.
SPECIFICATIONS
TYPES OF APPLICATION- Back plate of electronic devices (TV, readers, modems, servers, etc.)
- Pad print replacement solution
- Shutters
- Multilingual personalisation
- Polycarbonate
- UL94-VO Polycarbonate
- Lexan – Makrolon
- Semi-rigid vinyl
-
Cluster & back light filter
-
Gravic prints, caps and cuts backlight filters. Gravic also brings its experience and expertise to bear, by making its colour analysis laboratory available to its clients (LAB analysis / light transmittance / wavelengths / bandwidth / etc.)Backlight filters manage light diffusion.
They have a variety of functions:
- Giving a particular colour to a standard LCD display.
- Managing light diffusion from a display.
- To make LED backlighting consistent.
SPECIFICATIONS
TYPES OF APPLICATION
- Automotive displays
- Self-powered emergency lighting unit (BAES)
- BOX strips
- Transflectors
TYPES OF MATERIALS
- Polycarbonate
- PVC
- Polyester
- PMMA
- PET Lee Lightning filter
- PETG
- Plexiglas
-
Automotive Dashboard and Counters
-
With screen printing or digital printing, automotive counters require strong control of all the printing parameters of opacity, texture, transfer, light and colour. Gravic will provide you with a truly expert automotive screen-printing service. Both with digital printing and serigraphic printing, manufacturing automotive meters takes a high degree of technical precision and dedicated expertise to ensure a premium-quality finished product. With their wealth of 20 years’ experience working in the automotive industry, our teams are committed to making top-quality products, at the same time respecting all the applicable standards in the sector.
Our processes can be adapted to suit your specific order requirements: we can produce your automotive meters either using digital or serigraphic printing, and we also allow you to choose between polycarbonate or polyester as the base material. Depending on your needs, you can discover our full range of printing and technical cutting services for your automotive dashboards or any other front panel.
Our manufacturing process allows us to offer a range of products on sheets or rolls, depending on volumes. Selected adhesives can be screen-printed to make them the most competitive for this type of market.
Camera monitoring between printing and cutting ensures the dimensional compliance demanded by the automotive sector.As part of a new project, our expertise in this area now enables us to offer you your desired colour and opacity further upline in the production chain.
A final 100% control by camera is made before delivery.Serigraphic printing vs digital printing: what is the best choice of technique for you?
Serigraphic printing and digital printing each have their own merits for your automotive dashboard.
Serigraphic printing is a cost-effective procedure that uses a stencil for the design, as well as colours that are more resistant to long-term wear. On the other hand, digital printing can be used to create more intricate designs on an automotive meter with great precision.
Contact our experts for one-to-one advice and choose the technique that best meets your needs. We are available via email at [email protected].
Why choose Gravic as a provider of plastic front panel solutions?
Gravic, a specialist in printing and cutting techniques, comprises over 200 experts based at 4 sites spread across the world (France, Hungary, Tunisia, and China). Every year, we supply more than 500 million units to our 500 clients, including key figures in the automobile industry such as Peugeot. Thanks to strict tracking between the printing and cutting stages along with a thorough quality check procedure before all products are delivered, our finished automotive meters fully satisfy all the required standards. Our teams can also adapt their procedures to satisfy your specific project terms of reference and thereby supply you with a final product made with optimal precision for your needs.
What types of plastic front panels does Gravic offer?
Gravic offers a wide choice of front panels so that you can ensure the correct finish for your products while preserving their properties. Our flexible or rigid front panel cutouts ensure your devices are protected, while guiding users (by adding iconography for example) and contributing to your brand image (screen printing of your logos, colours, etc.).
Once your front panel is ready for use, Gravic provides you with a wide choice of rigid front panel decoration. These are designed to be resistant to liquids and scratches while remaining highly customisable, making them a complete solution for the creation of your front panels: design, cutting, screen printing.
What are the specifications of Gravic’s front and rear panels?
In order to find the front or back panel that best suits your criteria, Gravic offers a wide range of specifications to its customers that take into account the particularities of their products. In addition to the choice of material (polycarbonate or polyester front panel, metallic back plate, etc.), you can adjust the finish to obtain the desired visual effect: gloss, grained, matte or satin. The rigidity of your front panel will be linked to the material chosen as well as to its thickness: if you do not know whether a flexible or rigid front panel is best suited to your product, our experts are available to help you with your choice.
Visual and tactile functions are also available for the vinyl, Plexiglas and polycarbonate front panels: smoked coating for LEDs or backlighting, embossing for push buttons, anti-fingerprint coating, etc. We can thus offer high quality and fully functional front panels such as, for example, automotive dashboards and counters.
Do not hesitate to contact Gravic’s teams now to obtain additional information and get a quote.
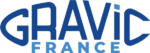
123, Zone Industrielle de l’Argile II, 06370
Mouans Sartoux, FRANCE
Tel. +33 (0)4 93 75 75 34
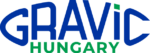
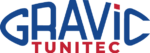
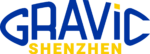
深圳市格瑞维克电子科技有限公司
深圳市南山区南山街道向南社区海德二道470号海德大厦A1002A
Shenzhen, CHINA