Industrial Lamination
Home -> Nos actualités -> Industrial Lamination
Industrial Lamination. Hot vs Cold Lamination
Laminating is a process of bonding two or more flexible packaging webs using a bonding agent. Webs can consist of films, papers or aluminum foils. Overall, an adhesive is applied to the less absorbent substrate web, after which the second web is pressed against it to produce a duplex, or two-layer, laminate.
Applications and types of lamination
Lamination is highly used to:
- Improve the products’ appearance,
- Serve as a protection for the product underneath and to become part of it,
- Add a scratch-resistant surface,
- Enhance the colour of printed images,
- Offer UV protection
Especially if you want a high-quality finish on your products.
Lamination covers a wide variety of applications in the packaging industries (including food), as well as for the manufacture of technical laminates for the solar energy and insulation panel sectors.
In order to understand which type of lamination would work best for your project it’s crucial to identify the end-use of the product and choose between a range of Cold and Hot Lamination technologies available today as they can both offer advantages and disadvantages. In this blog we’ve collected all the information you need to help in making your choice. Once you get to know the pros and cons of both techniques, you will be able to choose right and get the most from the Lamination solutions to benefit your business. Our experts are also available to guide you in making this key decision.
Hot and Cold Laminators
The main difference between Hot and Cold Lamination is the way the lamination machine activates and achieves better bond between substrate and adhesive material.
Cold Lamination
A cold laminator uses pressure and an adhesive to bond the product between plastics. The rollers of the cold lamination machines apply a lot of pressure and this is what’s required to finish the process.
Many users find that this process delivers superior quality without dealing with heating elements. Here are some advantages of the cold laminator over a hot one:
- Cold laminators require less maintenance and less set-up time. The machines are simpler, less expensive and easier to use. However, the machines are manual and do require a specialist to operate.
- The pressure applied by rollers of a cold laminator remove even the smallest bubbles that sometimes appear with a laminate.
- Cold laminators preserve the quality and colours of the printed document better than hot laminators. The heat of hot laminators can cause colour degradation and bleed.
- You can only laminate one side of a graphic with a cold laminator, which makes it a perfect choice for decals and adhesive decorations.
Hot Lamination
Hot Lamination machines use heat to melt or activate an adhesive material. This secures the plastic around the product.
The main advantage of hot lamination is that it provides more durable protection and a faster laminate job. Here are other points to know about the hot laminators:
- Hot Laminators have more application and include different materials like vinyl and other heat settings.
- Used materials for hot laminators are generally cheaper than the materials used in a cold laminator.
- Some colours, inks and materials might be damaged by the heat. However, there are special plastic laminates available to protect your products from the heat.
- The heat from a hot laminator can be extremely high and dangerous to use, so specialists should take high care while using it.
- It takes time and experience to learn how to properly use the hot laminator machines for your benefit. Within Gravic Group, we have specialists that are trained and experienced to use this particular technology.
Our laminating solutions
For over 50 years, Gravic Group has acquired knowledge and rich expertise in the laminating industry and we have a big variety of innovative solutions that work beautifully with any application. Our experts are available at any part of the world to discuss your needs and wishes. Whether it is to improve certain aspects of your existing process, to set up a new production, develop new products, or to make a bonding process review, Gravic Group has specialists and experts to assist you. Contact us for a full detailed consultation on your project.
We are grateful for our close collaboration, and we are committed to continuing to evolve and progress to meet your requirements!
Improve your life with Gravic!
Share this post:
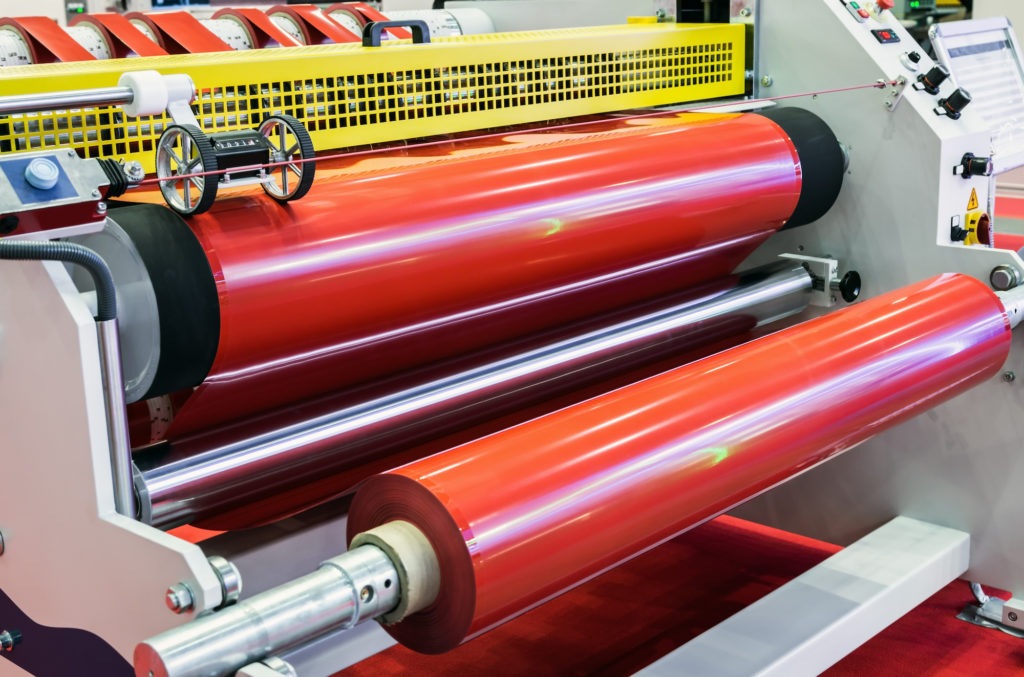