Foam Gaskets
Foam Gaskets and how to choose the right one for your business
Foam gaskets provide reliable sealing, cushioning, and insulation in a variety of applications. Foam is a very popular material in the industrial world thanks to its diverse features and functionalities. It’s been used almost in every industrial sector – from automotive and appliances to medical or lightning.
Foam gaskets are used in-between two hard surfaces to ensure a smooth process and improve the characteristics of appliances. Here are the main functions manufacturers are looking for when choosing foam gaskets:
- Insulation
- Cushioning
- Weather resistance
- Noise reduction
- Electrical absorption
- Fluid restriction
Open-cell and Closed-cell Foam gaskets
In order to understand which foam gasket will be best suitable for your project, it’s important to learn about the difference between open-cell and closed-cell foam gaskets.
Open-cell foams can take very light, flexible and adaptable forms. They have a very low compression set, meaning that it will always return to their original form and thickness even when compressed or weighed down by heavy items.
Closed-cell foam on the other hand have a higher compression set. This means that when compressed for long periods or with heavy items, they will not regain all of their original thickness. They are also highly water resistant due to the closed-off nature of their cells. These qualities make this type of foam perfect for outdoor appliances or for any product that might be exposed to the elements.
In summary, open-cell foam gaskets are primarily used in applications where shocks or vibrations are present and reduction is therefore required. Conversely, closed-cell foam gaskets are normally used in applications susceptible to outdoor conditions. In this case, environmental sealing is required to protect the mechanism from the elements.
Foam Gasket Materials
Foam materials are available in a broad range of thicknesses, hardness, densities and colors. Below you can find more information about the ones you’re most likely to encounter when selecting your gaskets.
Silicone foam
– available in both open-cell and closed-cell material
– lightweight in density with optimal flame resistance
– boasts a lower compression set than a typical silicone sponge
Silicone foam is usually used:
- Within outdoor sealing enclosures
- Within certain lighting enclosures
- To protect devices against vibration
- To protect and seal communications and electronics equipment
- To protect devices from shock and heat
Polyurethane foam
– open-cell and flexible
– cost-effective
– durable
– available in both fire retardant and anti-static forms
Typical range of applications:
- Dust and moisture sealing
- Component cushioning
- Thermal insulation
- Acoustic insulation
Polyethylene foam
– closed-cell
– available in 2 models – expanded or cross-linked
– available in conductive, anti-static, and fire-retardant forms.
The expanded model is strong and resistant. Naturally resistant to mold and mildew, it’s used in a range of packaging applications. It’s also vibration-resistant.
The cross-linked model features polyethylene foam that has been chemically cross-linked.
Compared to traditional polyethylene foam, this type of material has a smoother, more uniform finish. It also has stronger physical and chemical properties. Gaskets made with cross-linked foam possess excellent mechanical and thermal insulation, as well as chemical resistance.
Urethane foam
– has a low-density and open-cell material
– has an excellent thermal and acoustic insulation, as well as sealing, vibration resistance, energy absorption, and sound dampening
– flexible material and easy to fabricate and die cut.
Most commonly found in applications that undergo a substantial amount of wear and tear, including:
- Automobiles
- Appliances
- Electronics
- Industrial devices
Neoprene foam
Closed cell neoprene foam is highly versatile. It tends to have a lower density than other materials, along with improved water absorption properties.
- soft, durable, and form-fitting.
- commonly used in applications that require strong thermal and moisture insulation
How to choose the right foam gasket for your project?
Here are a few questions to help you understand the characteristics you require from your gasketing material:
- Think of your required application and function
- What type of application and function is required?
- Do you expect your gasket to seal gas or liquid?
- How do you intend to use it?
- Do you expect your gasket to keep its shape even after constant use?
- Application parameters
- What is the operating temperature of the application area?
- Internal pressure …
- UV and ozone exposure …
- Media (the fluid or gas that the gasket will be exposed to) …
- Are there any industrial parameters/regulations?
- The right size and shape
- It’s crucial to identify the correct size and shape that is required for your gasket.
Here at Gravic Group we offer the latest and most innovative die-cut solutions to be able to cut the tape and foam gaskets in exact custom sizes, shapes and formats. According to your needs, our expert will find the right solutions, materials and products. Contact us today and request a quote and a free consultation to discuss your project.
We are grateful for our close collaboration, and we are committed to continuing to evolve and progress to meet your requirements!
Improve your life with Gravic!
Share this post:
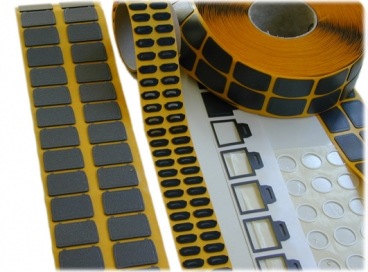